Client Location: Brooklyn, NY
Property Type: Residential Home
Service Provided: Crawl Space Vapor Barrier Installation, Wall Insulation, and Structural Sealing
Project Overview
A residential property in Brooklyn, NY faced issues related to moisture and inadequate insulation in its crawl space. The homeowner sought to improve the environment by installing a vapor barrier, upgrading wall insulation, and reinforcing the structural integrity of the crawl space. Zavza Seal LLC was chosen for the project due to our expertise in waterproofing and crawl space solutions.
Crawl Space Dimensions
- Floor Area: 728 sq. ft. (20′ x 30′ + 8′ x 16′)
- Wall Area: 180 sq. ft. (90’ x 2’)
Project Execution
1. Crawl Space Floor: Vapor Barrier Installation
Steps Taken:
- Soil Grade Preparation:
- The soil surface was smoothed to create a level base for the vapor barrier installation.
- 15-mil Vapor Barrier Installation:
- A 15-mil vapor barrier membrane was laid across the entire floor area (728 sq. ft.).
- The vapor barrier was extended 6 inches up the walls to create a seamless seal.
- Vapor Barrier Under Steel Beam:
- A 6” x 10’ steel beam within the crawl space was accommodated by carefully installing the vapor barrier underneath it to ensure complete coverage.
2. Crawl Space Walls: Insulation and Sealing
Steps Taken:
- Mortar Joint Repairs:
- Open mortar joints in the block walls were filled to restore structural integrity.
- Sill Plate Sealing:
- Joints in the sill plate were sealed with expanding foam sealer to prevent air leaks and moisture intrusion.
- Rigid Foam Board Insulation Installation:
- Rigid foam boards (supplied by the homeowner) were adhered to the walls using construction adhesives.
- Foam board adhesives were applied between the boards to ensure a tight seal.
- The foam boards, acting as additional vapor barriers, were hermetically sealed for maximum protection.
- Overlap for Enhanced Protection:
- The vapor barrier membrane from the floor was extended 6 inches up the walls and the foam boards were installed on top of this overlap for complete moisture protection.
- Inspection Clearance:
- Per the owner’s request, a 6-inch clearance was left between the foam boards and the sill plate for inspections, exceeding the InterNACHI standard of 3 inches.
3. Batt Insulation Replacement
Steps Taken:
- Old Batt Insulation Removal:
- Approximately 120 sq. ft. of deteriorated batt insulation was removed and disposed of responsibly.
- New Batt Insulation Installation:
- New batt insulation (provided by the owner) was installed to improve thermal efficiency.
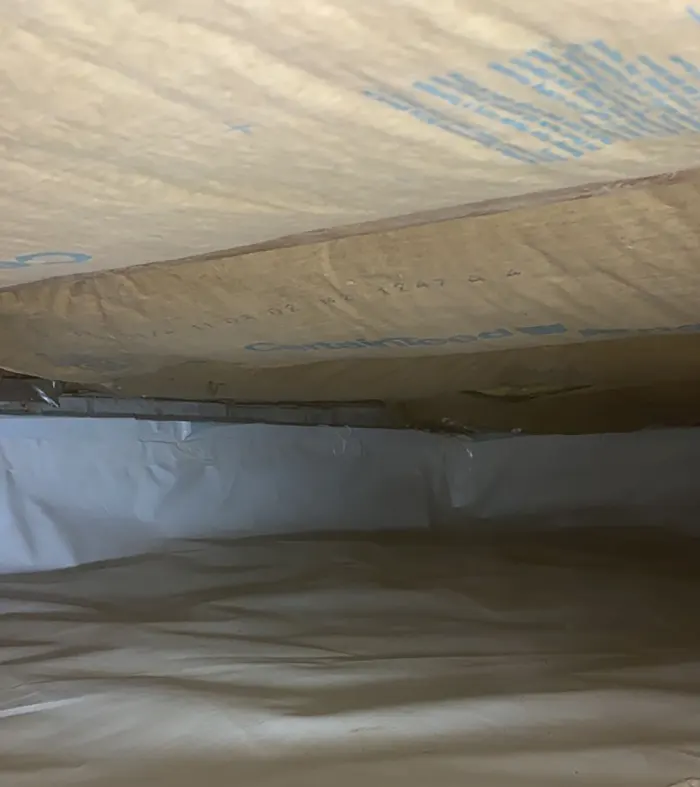
The crawl space after insulation and vapor barrier installation
Project Results
- Moisture Protection:
- The combination of the 15-mil vapor barrier and rigid foam boards created a robust moisture barrier, significantly reducing dampness and humidity in the crawl space.
- Enhanced Insulation:
- The new rigid foam board insulation and batt insulation improved energy efficiency and maintained consistent indoor temperatures.
- Structural Integrity:
- Sealed mortar joints and sill plates reinforced the crawl space structure, preventing potential damage from moisture and air leaks.
Client Satisfaction
The homeowner was highly satisfied with the results, noting improved air quality, reduced moisture, and enhanced energy efficiency. Zavza Seal LLC‘s attention to detail and ability to customize the project to the owner’s needs reinforced our reputation for quality service in Brooklyn, Long Island, and Queens.
Why Choose Zavza Seal LLC for Crawl Space Waterproofing in Brooklyn?
- Expert Solutions: Customized waterproofing and insulation strategies tailored to your property’s needs.
- Attention to Detail: Adhering to client requests and industry standards.
- Local Knowledge: Serving Brooklyn, Long Island, and Queens with years of experience in crawl space repairs.
Contact Zavza Seal LLC
Protect your home’s crawl space with expert waterproofing and insulation solutions.
📞 Call Now for a Free Consultation!
🌐 Visit: ZavzaSeal.com