Introduction:
This case study details the successful repair of a concerning vertical crack in a Brooklyn basement, undertaken by Zavza Seal LLC. The extensive crack, measuring approximately 15 feet from floor to ceiling, posed a significant threat to the structural integrity of the foundation and allowed water infiltration. Through a meticulous process of inspection, diagnosis, and repair, Zavza Seal LLC restored the basement wall and provided the homeowner with lasting peace of mind.
Client Concerns:
The homeowner contacted Zavza Seal LLC after discovering a large vertical crack running along the entire east side of their basement cinder block wall. Their primary concerns were:
- Water Leakage: The crack allowed water seepage into the basement, potentially leading to moisture damage, mold growth, and a damp, unpleasant environment.
- Structural Integrity: The extensive size of the crack raised concerns about the structural stability of the foundation walls.
Onsite Inspection and Assessment:
A certified Zavza Seal LLC inspector visited the property to assess the situation firsthand. The inspection included:
- Visual Examination: A thorough visual examination of the crack, noting its size, location, and any visible signs of water damage.
- Moisture Detection: Utilizing moisture detection tools to identify any hidden moisture issues within the wall.
- Foundation Assessment: Evaluating the overall condition of the foundation to determine if the crack was an isolated issue or indicative of a broader structural problem.
Diagnosis:
Based on the inspection findings, the Zavza Seal LLC team diagnosed the problem as a large structural crack in the cinder block wall. This crack required immediate attention to prevent further water infiltration and potential structural concerns.
Proposed Solution:
To address the crack and restore the basement wall, Zavza Seal LLC recommended a comprehensive repair plan involving several key steps:
- Surface Preparation: Extensive surface preparation using diamond blades to remove paint, loose material, and any foreign objects from the affected area. This creates a clean and well-bonded surface for the repair materials.
- Crack Stitching: Cutting deep slots perpendicular to the crack at 12-inch intervals throughout its entire length. These slots act as channels for the structural epoxy and carbon fiber stitches.
- Structural Epoxy Injection: Filling the newly cut slots with a high-strength structural epoxy resin. This epoxy reinforces the crack from within, preventing further movement and water infiltration.
- Carbon Fiber Reinforcement: Installing non-corrosive carbon fiber stitches within the epoxy-filled slots. These high-tensile strength stitches provide additional structural support, literally pulling the crack closed with a capacity of 6,500 pounds each.
- Waterproofing Membrane: Applying a thick coat of 7,000 PSI waterproofing cement to the entire affected area. This waterproof barrier prevents future water seepage through the crack.
- Reinforced Mesh and Finishing Touches: Laying a layer of reinforced fiber mesh 4.5 oz. on top of the wet waterproofing cement for added strength. Finally, applying a second coat of waterproofing cement to ensure complete coverage.
- Painting: Completing the project with a fresh coat of paint on the repaired area, restoring a finished appearance to the basement wall.
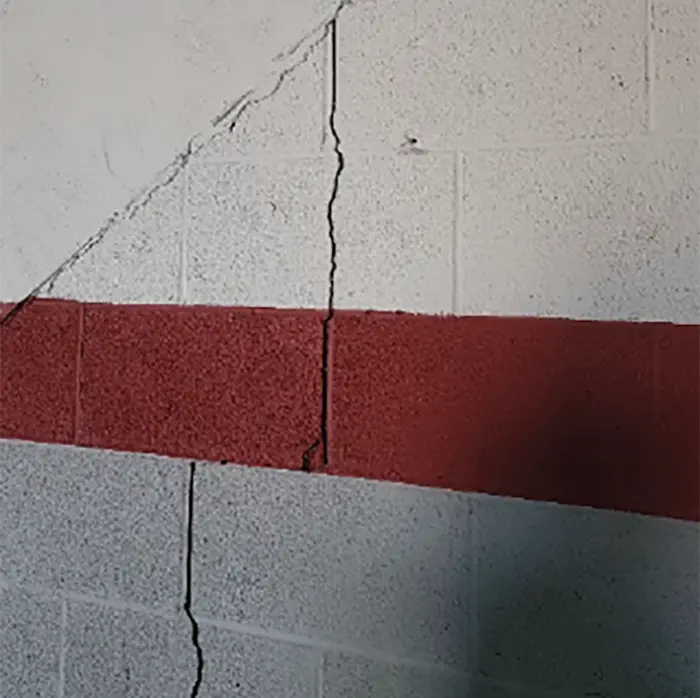
Vertical cracks in the basement wall
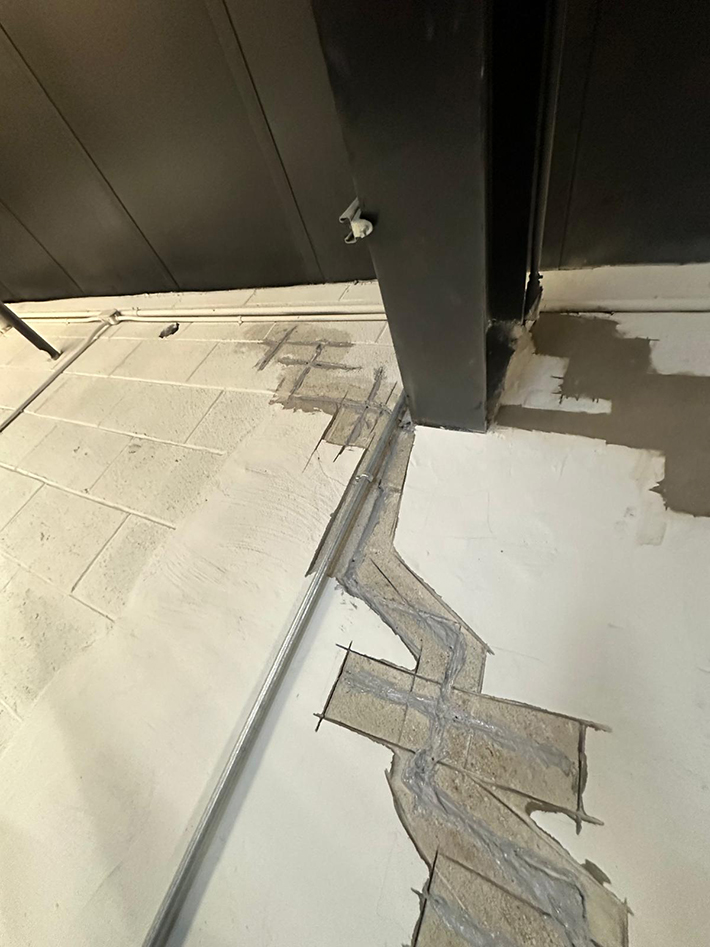
Deep slots perpendicular to the crack at 12-inch intervals are dug and filled with structural epoxy and carbon fiber stitches.
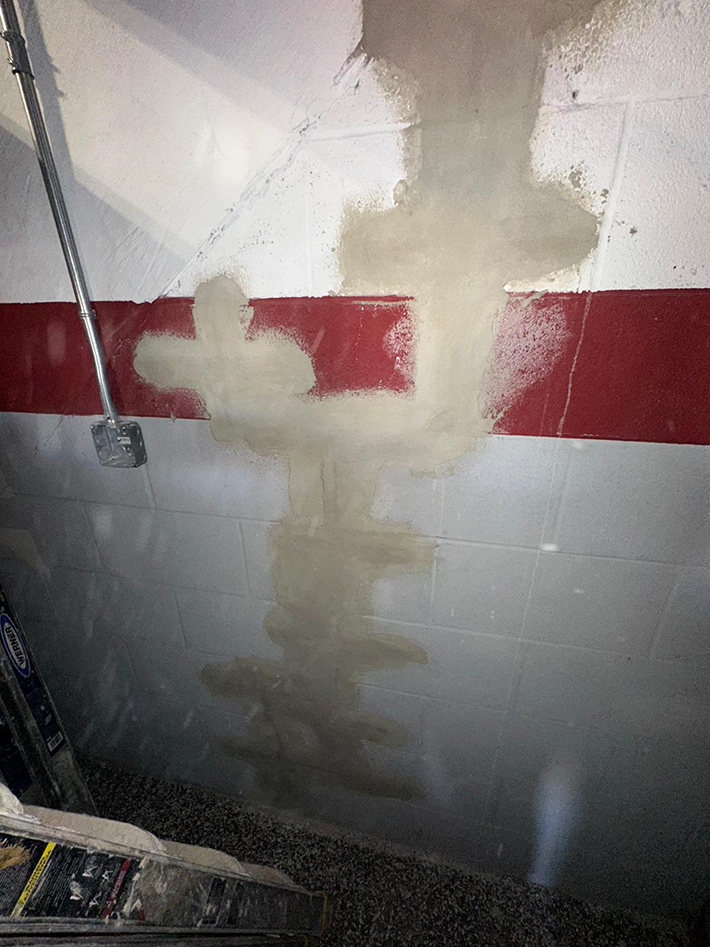
After laying a layer of reinforced fiber mesh 4.5 oz. on top of the wet waterproofing cement for added strength we painted the repaired area.
Project Execution:
The Zavza Seal LLC team meticulously followed the proposed repair plan, ensuring each step was completed thoroughly and according to industry standards. The homeowner was kept informed throughout the process and had the opportunity to ask questions or address any concerns.
Project Outcome:
The completed project successfully addressed the structural crack and water infiltration issues. The repaired wall exhibited increased structural integrity and a waterproof barrier against future moisture problems. The homeowner expressed satisfaction with the thoroughness of the repairs, the professionalism of the Zavza Seal LLC team, and the overall positive transformation of their basement.
Conclusion:
This case study demonstrates the expertise of Zavza Seal LLC in addressing complex foundation issues like large structural cracks. By combining thorough inspection, accurate diagnosis, and a multi-step repair process, Zavza Seal LLC effectively restored the Brooklyn basement wall and provided the homeowner with a safe and dry environment.
Additional Notes:
- This case study highlights the importance of not ignoring foundation cracks. A seemingly minor crack can worsen over time and lead to significant structural and water infiltration problems.
- Early detection and professional repair are crucial for preventing costly future repairs and potential foundation failure.
- Zavza Seal LLC offers free consultations to homeowners in Long Island, Queens, and Brooklyn to assess foundation concerns and provide personalized repair solutions.
This case study not only showcases the technical aspects of the repair but also emphasizes the importance of clear communication and client satisfaction throughout the process. By combining expertise with a commitment to customer service, Zavza Seal LLC delivers exceptional results for homeowners facing foundation challenges.